Can You Really ‘burn’ Steel?
Talking about steel always brings forward certain images and one of the most enduring is that of the foundry. People often imagine huge containers full of yellow hot metal, being poured or extruded into sections – and the chances are that if you asked people what it’s like to work in such an environment, they’d reply “noisy” and “incredibly hot”.
It’s true that metalwork, even from the earliest times, has always involved working with temperatures that people find uncomfortable. The first people to heat Malachite in order to extract the copper had to basically form extremely hot fires, burning at close to 1,000°C. Blacksmiths’ shops have always had a fire pit to heat metals and make them more malleable, so many people would be astonished that it’s possible to overheat metals and effectively ‘burn’ them!
Our knowledge in metallurgy is as advanced as it’s ever been, to the point where we can adjust, tweak and change the makeup or treatment of certain metals to make them perfect for any number of specific uses. Those who have experience of High Speed Steels, Martensitic Stainless Steels or Spring Steels know that using the right material for the job is vital, and it relies on the right chemical make-up and fabrication processes to get just the right characteristics – effectively making each grade of steel has its own ‘recipe’.
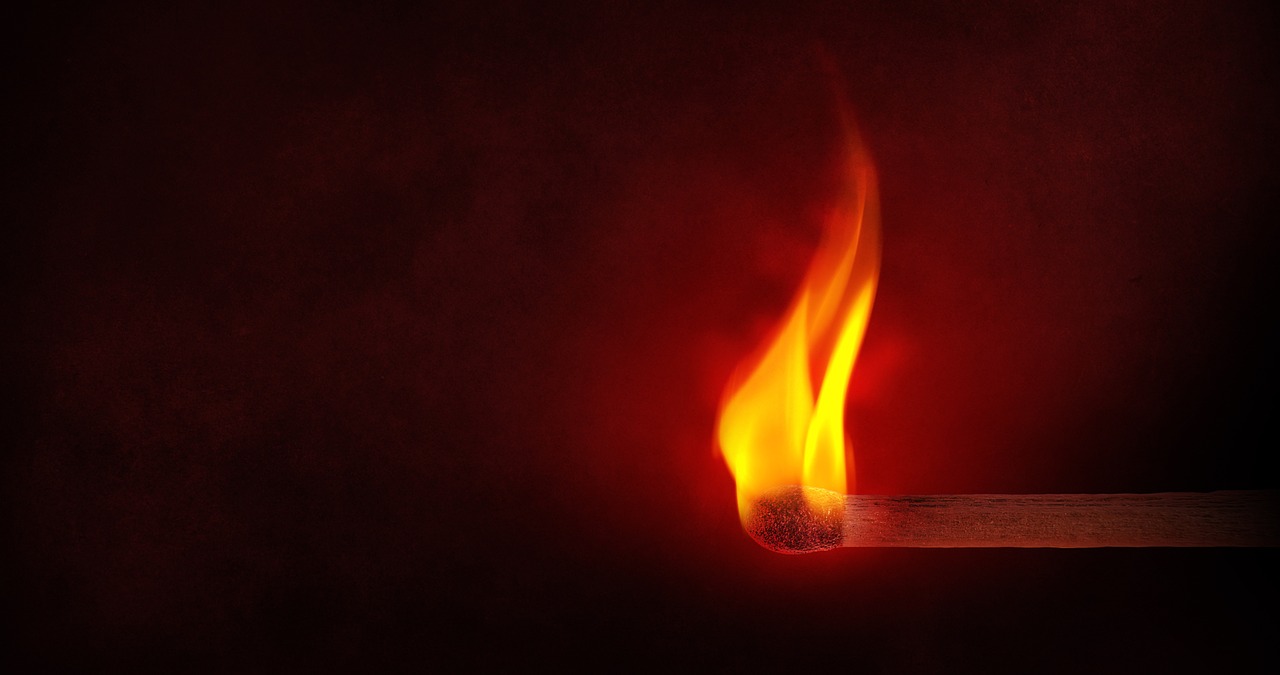
In almost the same way that using one bunch of ingredients can give us pancakes, Yorkshire puddings, waffles or a Victoria Sponge, altering the treatment and quantities in metals can give us wildly different results. For steel and other kinds of low alloy metals, there’s a threshold of approximately 1200°C that, once exceeded, can negatively affect the mechanical properties.
‘Burning’ the metal by applying too much heat over a prolonged period reduces the desirable mechanical properties of the final material. Depending on the grade of steel, it can prevent the steel from hitting the required hardness level so that it is more easily ground away or won’t withstand impact. In some cases, it can make the whole product brittle and prone to fracturing, or possibly create uneven zones of brittleness that crack at lower tolerances. It’s also possible for the surface of the material to form itself into blobs of hard and soft spots throughout, making it pitted and bobbled.
In the same manner as you can burn the outside of a cake while the inside remains raw, applying too much heat in too short a time can negatively affect the properties on the outside of steel without actually having the desired effect at the core of the material! This is why proper temperature control is key. Using the right amount of heat, monitoring both the equipment and the metal inside and controlling the cooling environment prevents negatively affecting the final product.
Although the image of the foundry is often thought of as an extreme environment in terms of high temperature and unforgiving heat, it’s worth remembering that only as much heat is used as necessary to create the perfect steel. Whether you’re baking at 220°C or forging at 1100°C, using the right ingredients and the right method will give you the perfect outcome!