D2 tool steel information – over 100 years at the cutting edge
D2 is a high carbon, high chromium, molybdenum vanadium alloy tool steel. After hardening D2 achieves a high hardness with high compressive strength. It has excellent dimensional stability in hardening which makes this a quality through hardening steel with good retention to tempering. D2 is very popular for tolls that require very high wear resistance combined with moderate toughness and shock resistance. D2 has good through hardening properties and maintains good stability during heat treatment. It can also provide a measure of corrosion resistance when polished.
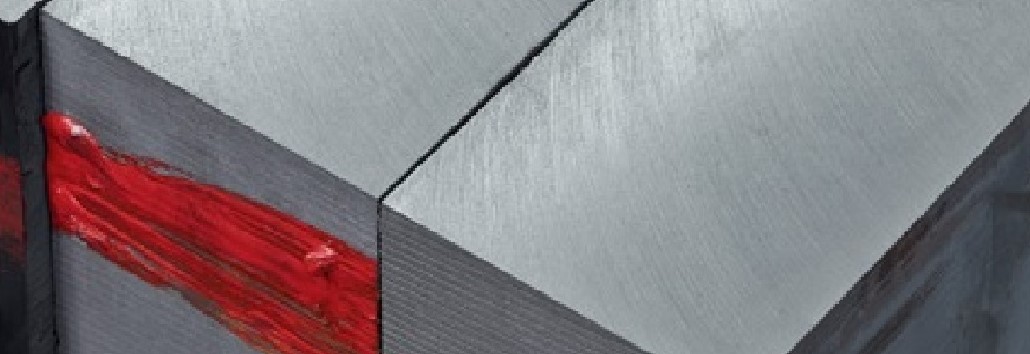
D2 Typical Analysis
Carbon | 1.55% | Chromium | 12.00% |
Manganese | 0.45% | Molybdenum | 0.85% |
Vanadium | 0.80 | ||
D2 steel equivalents
As a wideley used tool steel grade many countries around the world started producing their own versions of this high carbon high chromium tool steel. With some subtle differences in composition these are some examples of the foreign equivalents to D2
Country | Standard | Specification |
---|---|---|
UK USA ” ” ” Germany ” Eurnorm France Sweden Spain Japan Russia |
BS4659 AISI SAE ASTM UNS Werkstoff DIN – AFNOR SIS UNE JIS GOST |
BD2 |
D2 Machinability
When milling D2 with carbide tips a roughing operation can be carried out at cutting speed of approximately 100-140 Vc m/min with finishing operation speed of approximately 120-160 Vc m/min. Drilling with a high speed steel drill bit can be done at an approximate speed of 10 Vc m/min. For rough turning a cutting speed of approximately 100-150 Vc m/min and fine turning 150-200 Vc m/min.
D2 Round Bar
D2 is supplied in a large range of round bar sizes starting at 10mm up to about 500mm in diameter. West Yorkshire Steel can supply as full bars or bandsaw cut to your specific requirements.
D2 Flat Bar / D2 Plate
D2 flat sections be supplied from bar or plate and when non stanards sizes are required these can be produced by cross cutting from large forged machined billet.
D2 Flat Sheet
D2 sheet is supplied in a limited range of thicknesses.
D2 Ground Flat Stock
Precision ground flat stock / gauge plate can be produced using D2 tool steel. Subject to size, suitability and availability pieces can be produced in approximately 2 to 3 weeks. Standard and non-standard sizes are available.
D2 Heat Treatment
Popular heat treatment process for D2 include the following:-
Hardening & Tempering
Vacuum Hardening
Nitriding
Nitrocarburising
Induction Hardening
Flame Hardening
Stress Relieving
Annealing
Many factors should be considered when hardening D2. Heat treatment temperatures, including rate of heating, cooling and soaking times will vary due to factors such as the shape and size of each D2 steel component. Other considerations during the heat treatment process include the type of furnace, quenching medium and work piece transfer facilities. Heat treatment specialists can provide for full guidance on heat treatment of D2 tool steel.
D2 Hardening
The most common heat treatment process for D2 is vacuum hardening, carried out under protective atmospheres this helps avoid oxidation or decarburisation of the component surface.
D2 is also suitable for air hardening or oil hardening. Pre heating of the D2 tool steel component is required. Heat to 750-800°C and allow to fully soak at this temperature. Then raise the heat up to 1000-1040°C for air cooling, or 980°C for oil quenching. Soak thoroughly at the temperature for thirty minutes per 25mm of ruling section, then cool or quench accordingly. It is important not to exceed 1040°C when heating for hardening.
D2 Tempering
Double tempering is recommended to help reduce the quantity of retained austenite. Tempering of D2 tool steel should be done with the least possible delay after hardening, preferably when the tools are include the at a temperature of 50-70 °C. Select a suitable tempering temperature, bearing in mind
the service requirements. Heat slowly and uniformly. When the D2 component has reached the desiredtemperature, soak for at least one hour per 25mm of section (with a minimum holding time of 2 hours). The second tempering should be a repetition of the first. Martempering can also be done on this steel grade.
Temperature [°C] | 150 | 200 | 250 | 300 | 350 | 400 |
Hardness [HRc] | 62-61 | 61-60 | 60-59 | 57-56 | 56-55 | 56-55 |
D2 Stress Relieving
When tools made from D2 tool steel are heavily machined, ground or otherwise subjected to cold work, the relief of internal strains is advisable before hardening to minimise the possibility of distortion during heat treatment. Stress relieving should be done after rough machining. To stress relieve, heat the D2 to 600-650°C. Soak well and cool in the furnace or in air. The tools may then be finish machined before hardening.
D2 Annealed / Annealing
In standard supply D2 is delivered in the fully annealed condition. As a high carbon high chromium alloy tool steel this makes for easier machining. For guidance only annealed D2 will be in the region of 220 Hardness Brinell (HB). This hardness can vary due to rate of heating and cooling, also other factors such as the shape and size of the steel being annealed.
If the steel has been forged or hardened it can be re-annealed. To fully anneal D2, heat slowly and uniformly to 900°C. Soak for three to four hours and allow to cool in the furnace to room temperature. Re-heat to 800-1040°C and again soak for three to four hours. Allow to cool in the furnace to room temperature.
D2 Final Grinding
Select the correct grade of wheel in consultation with the grinding wheel manufacturer. Ensure the grinding wheel is in good condition by means of a suitable dressing tool. Wet grinding is a preferable option using a copious supply of coolant. If dry grinding is resorted to then use a very soft wheel. When tempered at lower temperatures components can suffer grinding cracks.
D2 Corrosion Resistance
D2 has a high chromium content similar to certain 400 series stainless steel grades. For a tool steel it has reasonable corrosion resistance and is sometimes known as a ‘semi stainless’. A polished surface aids the corrosion resistance properties of D2.
D2 Typical Physical Properties
Thermal Expansion Conductivity Modulus of Elasticity Specific Heat Density |
10.4 x 10-6/°C 20 W/(M K) 21000 Mpa 460 J/kgK 7.7 kg/m² |
20-100°C 20°C 20°C 20°C 20°C |
---|---|---|
|
History of D2 Tool Steel
There is a very strong sense of history of tool steel manufacturers in Yorkshire stretching back to the late 19th century. Quite often the compositions of different tool steel grades were held secret and handed down from one generation to the next. In Sheffield the majority of tool steel manufacturers considered their products to be the best. They believed the British manufactured tool steel to be far superior to tool steels produced in the USA. Indeed many early producers of tool steel in the USA were either born in or trained in Yorkshire. In the early 20th century many producers of tool steels in the UK sold a high carbon high chromium type tool steel, very similar to the D2 grade we know today. Each producer had their own unique name and many claimed theirs to be the best high carbon high chromium steel on the market We list below some of the historical brand names associated with D2, and to this day we occasionally receive enquiries requesting these grades.
Many eminent metallurgists and steel makers at this time were experimenting with steels with various percentage levels of high carbon and high chromium. Well-known historical pioneers in steel, such as Robert Hadfield (the metallurgist noted for his discovery of high manganese work hardening steel) and Harry Brearley (who discovered stainless steel) were very interested in the metallurgy of tool steels, both of them working on varying alloying elements in steel, including high carbon and high chromium contents – a key element in both D2 tool steel and stainless steel. The names of many other early inventors of tool steel grades may never be known. It is highly probable that a D3 type tool steel was developed initially, high carbon, high chromium and capable of achieving a high hardness up to ~64 Rockwell with good wear resistance.
It may be that a D3 type material was more common at this time, but there were issues with D3, at high hardness it could be prone to chipping or cracking. A slight reduction in carbon content and the addition of vanadium brought about D2. D2 does not achieve the high hardness of D3 but does have better toughness and shock resistance. These characteristics could provide a longer life to a tool and is why D2 is one of the most highly used tool steels in the world today.
Here are some examples of companies who were producing D2 type tool steel and their brand name:-
Balfour & Darwins Beardshaw Steels Ltd Richard W Carr Ltd Firth Brown Ltd Hadfields Ltd George H Cook & Co Ltd Hall & Pickles Ltd Jessops Saville Ltd Jonas & Colver (Novo) Ltd Macreadys Ltd Kayser Ellison Ltd Samuel Osborn & Co Ltd FM Parkin Ltd Walter Somers Ltd HJ Stone Steel Ltd Stora Steel Ltd Timken Latrobe Steel |
SC25 CDV2 69S Diehard Standard Hecla 159 KMV Vital-X H42 NRM HCHC KEA180 GN FMP36 Somcold CS13M Extra Stora 364 Olympic |
|
About West Yorkshire Steel Co Ltd
We’ve learnt a lot about steel in over 45 years of business. We’re very friendly and we really strive to help our customers. With a wealth of experience and knowledge, we supply D2 and other quality steel specifications in accordance with our ISO 9001 policies. Whilst many things have changed in the steel industry it is always our commitment to provide quality and service, with our dedication to total customer satisfaction. It is our years of experience which keeps us at the forefront of the special steel sector.
Over the years we have seen many steel companies come and go. We have seen much of our competition consumed by merger mania, hoping that bigger is better; at West Yorkshire Steel we remain a family run business committed to constantly providing a friendly and reliable service. The most valuable possession we own is our reputation for quality and service.