EN24 steel information – strength in steel for over 100 years
What is EN24? EN24 is a 1.5% nickel, 1% chromium, 0.2% molybdenum alloy steel which has a long history dating back over 100 years. EN24 can be heat treated to a wide range of tensile strengths from 850-1000 N/mm² (‘T’ condition) up to 1550 N/mm² (‘Z’ condition). Heat treated EN24 offers high tensile strength combined with good ductility and resistance to shock. At low temperatures good impact values can be obtained. In this blog we explain a little about the characteristics and history of this well established steel grade.
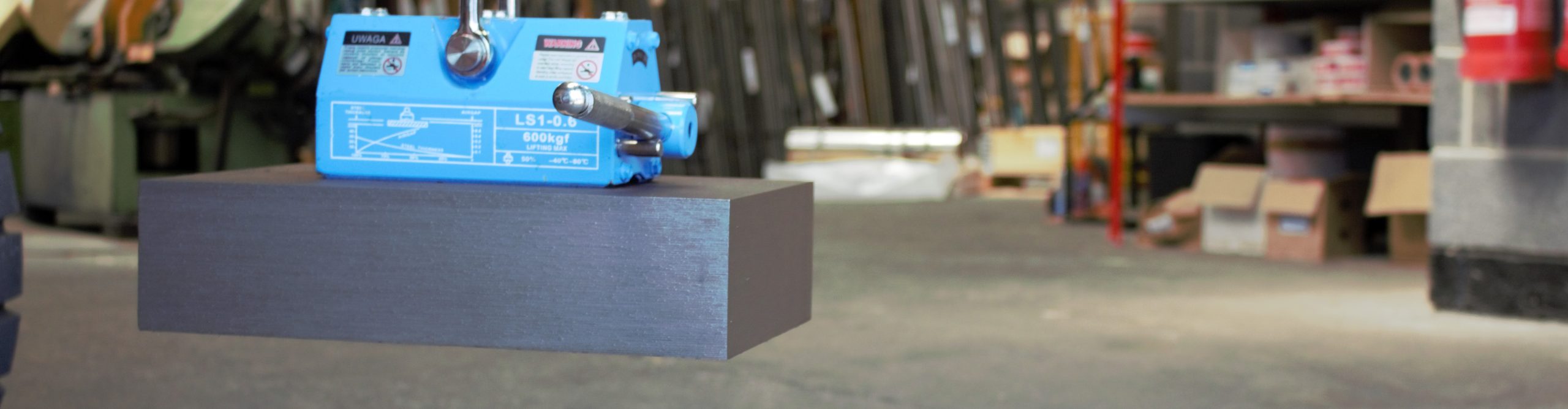
EN24 Typical Analysis
Carbon | 0.35-0.45% | Silicon | 0.10-0.35% |
Nickel | 1.30-1.80% | Manganese | 0.45-0.70% |
Chromium | 0.90-1.40% | Phosphorous | 0.05% max |
Molybdenum | 0.20-0.35% | Sulphur | 0.05% max |
EN24 steel equivalents
Being such a popular alloy steel grade many countries around the world started producing their own versions of a nickel chrome moly high tensile steel. With some subtle differences in composition these are some examples of the foreign equivalents to EN24
Country | Standard | Specification |
---|---|---|
USA Germany ” France Sweden Spain Japan BS |
AISI/SAE DIN Werkstoff AFNOR SIS UNE JIS Aerospace |
4340 |
EN24 steel properties
When used for applications in its heat treated condition EN24T combines high tensile strength with shock resistance. It is easy to work and can be forged or stamped without difficulty. EN24 is machinable in the annealed condition or when hardened and tempered.
EN24 Machinability
The machinability of EN24 in the annealed condition is approximately 53% of that for mild steel (070M20). When supplied as EN24T the machinability is approximately 35%-40% of that for mild steel (070M20).
EN24 applications
When first becoming more prevalent back in the early 1900s EN24 was classified as a wrought steel for automobiles and aircrafts and as such was used to produce numerous parts and components for these industries. It is most popular as EN24T and with good high tensile properties in T condition it is used widely in the manufacturing sector. Some examples of applications include:-
• Power transmission gears and other gears requiring maximum hardness.
• Cranks, axles, propellor and gearbox shafts requiring good high tensile properties.
• Connecting rods, special cranks and other parts required to be stiff and yet retain a high degree of toughness.
• Bolts, screwed parts, stub axles, swivel arms required very tough.
• Plastics and rubber moulding industry parts for moulds, hob retaining rings, stop pins.
• Structural components with good high tensile needs.
EN24 Round Bar
EN24 is produced in a large range of round bar sizes starting at 6.35mm up to about 1 metre in diameter.
EN24 Flat
EN24T flat sections can be produced by cross cutting from large forged machined billet.
EN24 Heat Treatment
EN24 can be heat treated using various processes. Conventional hardening and tempering required the steel to be slowly and thoroughly heated to 830-850°C followed by immediate quenching in oil. Tempering is done as soon as the steel reaches room temperature. If hardening from T condition is required it is recommended to fully anneal prior to heat treatment. Standard annealing of EN24T can be carried out by heating slowly and uniformly to
840-860°C, cool in the furnace to 580°C then allow to cool to room temperature.
Heating, cooling and soaking times can vary due to factors such as the size and the shape of the component. Heat treatment providers can offer a full range of heat treatment processes including the following:-
Hardening & Tempering
Plasma Nitriding
Nitriding
Case Hardening
Carburising
Nitrocarburising
Induction Hardening
Flame Hardening
Stress Relieving
Annealing
Typical Mechanical properties for EN24
Condition | Tensile N/mm² |
Yield N/mm² |
Elongation % |
Izod KCV J |
Hardness Brinell |
---|---|---|---|---|---|
T | 850-1000 | 650 | 13 | 35 | 248-302 |
U | 925-1075 | 755 | 12 | 42 | 269-331 |
V | 1000-1150 | 850 | 12 | 42 | 293-352 |
W | 1075-1225 | 940 | 11 | 35 | 311-375 |
X | 1150-1300 | 1020 | 10 | 28 | 341-401 |
Y | 1225-1375 | 1095 | 10 | 21 | 363-429 |
Z | 1550 | 1235 | 5 | 9 | 444 |
(*subject to ruling section)
EN24 is commonly supplied as EN24T or EN24U. For EN24V, EN24W, EN24X, EN24Y & EN24Z material should be fully annealed before heat treating to any of these conditions.
For further information on hardness equivalents use our steel hardness converter
EN24 Annealed
EN24 when annealed has no specific mechanical or hardness values. For guidance only it will be in the region of 220 Hardness Brinell. This hardness can vary due to rate of heating and cooling, also other factors such as the shape and size of the steel being annealed.
Welding EN24
EN24 can be welded in the annealed condition but welding of EN24T (its normal supply condition) or higher tensile is not recommended. Cracking can occur as the high tensile properties of the steel can be affected by the heat of the weld. It is not recommended to weld after any hardening treatments such as nitriding, case, flame or induction hardening. To weld EN24 annealed it is recommended to us use low hydrogen electrodes, heat to approximately 200-250°C and hold at this heat during the welding process. It is strongly advised to stress relieve after the piece has cooled to room temperature. This information provided is for guidance only and we always recommend you contact your welding consumables supplier who should provide you full assistance and information on welding EN24.
Stress Relieving EN24
After welding or when components are heavily machined, ground or otherwise subject to cold work, stress relieving will be beneficial prior to hardening. To stress relieve EN24 heat carefully to 650-670°C, soak well before cooling in the furnace or in the air.
EN24 steel history
EN24 has a very long history. We believe it was first produced as a nickel chrome steel in the many steel mills of Sheffield dating back to the late 19th century. In to the early 1900s many of the numerous steel producers in and around Sheffield were manufacturing a 1.5% nickel 1% chromium (sometimes with the addition of a 0.2% molybdenum) alloy steel but identifying and branding their version with their own unique name. Each mill would often market their brand as the best quality produced steel.
In the gallant days of British Steel manufacturer it was deemed necessary (rightly so) to catalogue the most commonly used range of steels in the UK, namely BS970 EN steels. Chemical analysis and physical properties were clearly stated which gave a comprehensive user view of what was require for a specific application. This was a forward step for the many associations who took part, confirmed by the British Standards Institute. It is obvious that at the time of formulation many of the ‘special steel’ manufacturers desired to hide their compositions under their secret pseudonyms (see below). Some of these names appeared for many years and are occasionally mentioned these days. A retired employee of West Yorkshire Steel spent many long house revealing and cataloguing the similar chemical compositions and properties when he worked in the Research Laboratories of Kayser Ellison Ltd.
Here are some examples of who were producing and their brand name:-
Manufacturer | Brand name for their nickel chrome moly steel | |
---|---|---|
B Huntsman Ltd Samuel Osborn Ltd A Balfour & Co Ltd Richard W Carr Ltd English Steel Coprpration Ltd Thomas Firth Ltd Samuel Fox & Co Ltd Hall & Pickles Ltd Jonas & Colvar Ltd Jessop Saville Ltd Sanderson Brothers & Newbold Ltd Kayser Ellison Ltd Watson Saville & Co Ltd Spear & Jackson Ltd |
NCM1 NF SD20 Plutonic 553 PLMB/1 NCM1 Fox 171 Versatile SGWI G5 Special Sanbold24 KE805 CNC0H3 Spear 524 |
|
EN24 first gained official recognition in 1916 published in the British Engineering Standards Association (BESA) publication British Standard Specifications for Wrought Steels for Automobiles and given the name ‘E.S.C. 1 ½ PER CENT NICKEL-CHROME STEEL’
The BESA later became part of the British Standards Institution (BSI) and in their publication in 1924 of the British Standard Schedule of Wrought Steels for Automobiles the ESC grade was renamed BS Steel No 5005/503
Prior to World War II efforts were made to rationalise steel specifications to reduce the wide number of steels being produced. But it wasn’t until after the war had started that this idea came to fruition. The Technical Advisory Committee (TAC) of the Aircraft Special & Alloys Steels Committee was set up to reduce the substantial number of steel specifications being produced. The task of the TAC was to prepare and publish a limited number of special and alloy steel specifications, calculated to cover the whole of the requirements of the fighting services and industrial usage. Publications of BS970 and BS971 in 1941 provided information about the new TAC grades. The BS971 edition providing comprehensive technical information for the designers and engineers of that era.
It is at this time that the first mention of EN24 is made under the TAC reference number TAC/13. It is often asked what does the EN stand for in EN24. It is our belief from working with many universities and libraries in our long history that EN stands for ‘Emergency Number’. Despite our large library on steel grades and specifications we can find no written record to confirm this.
For the new TAC/13 a small molybdenum content was now included in the specification. The addition of molybdenum to EN24 significantly helped its hardening capabilities. EN24 could be hardened up to 100 tons tensile, but the TAC publication made specific mention of the ruling section of the steel. To achieve 100 tons tensile (‘Z’ condition) it had a limited ruling section of 1 ⅛” but EN24 was becoming more popular as EN24T with its superior limited ruling section of 6”.
In the 1941 the BSI published War Emergency British Standard Schedule 970 : 1942. EN24 was listed with the following caveat ‘by agreement between purchaser and manufacturer the molybdenum may be omitted’).
Some BS970 grades were superseded and updated over the years. We have original copies of the 1947, 1950 and 1955 editions of the BS970 publications but no changes or amendments were made to EN24 until 1970.
The Revision of BS970
In 1970 a major change was made to all BS970 steel specifications. EN24 was now to be known as 817M40. Nearly all EN grades had a specification name change. The BSI explained that ‘in place of the EN series, a more versatile six-character designation has been introduced’. It is a matter of opinion but at West Yorkshire Steel, over 50 years since the change of name to 817M40, we find most customers prefer to use the old adage EN24!
About West Yorkshire Steel
We’ve learnt a lot about steel in over 50 years of business. We’re very friendly and we really strive to help our customers. With a wealth of experience and knowledge, we supply EN24 and other quality steel specifications in accordance with our ISO 9001 policies. Whilst many things have changed in the steel industry it is always our commitment to provide quality and service, with our dedication to total customer satisfaction. It is our years of experience which keeps us at the forefront of the special steel sector.
Over the years we have seen many steel companies come and go. We have seen much of our competition consumed by merger mania, hoping that bigger is better; at West Yorkshire Steel we remain a family run business committed to constantly providing a friendly and reliable service.