There’s a Name for Processes Like That
While steel and metallurgy is ever moving forward as the underpin of the futuristic society; a world of glass-and-steel skyscrapers and materials created in the laboratory, it’s sometimes easy to forget that where we are now is the culmination of literally thousands of years of progress. There are processes, ideas and words that have been around for a long time – so long that we may have forgotten where they came from and end up sounding a little strange.
Some of these technical terms survive because they refer to a specific process and there’s still a need for the individual word, even if it’s under a broader heading, such as the heat treatment of steel. Heat treatment is actually very complex simply due to the number of changes that occur during the process and how different each of these can be.
Annealing is where a steel is heated and held at its best temperature in the furnace before being allowed to cool very slowly to make it as soft as it needs to be so that it can be machined or worked on when cold. This also includes Spheroidising which is annealing for high carbon steels that otherwise couldn’t be machined.
Hardening is as it sounds, but in this case refers to heating the steel fractionally above its critical range before quenching, which is removing all heat and cooling in liquid, such as oil or water. Induction hardening works on a similar process, but aims to harden the surface of a metal by high-frequency induction before quenching.
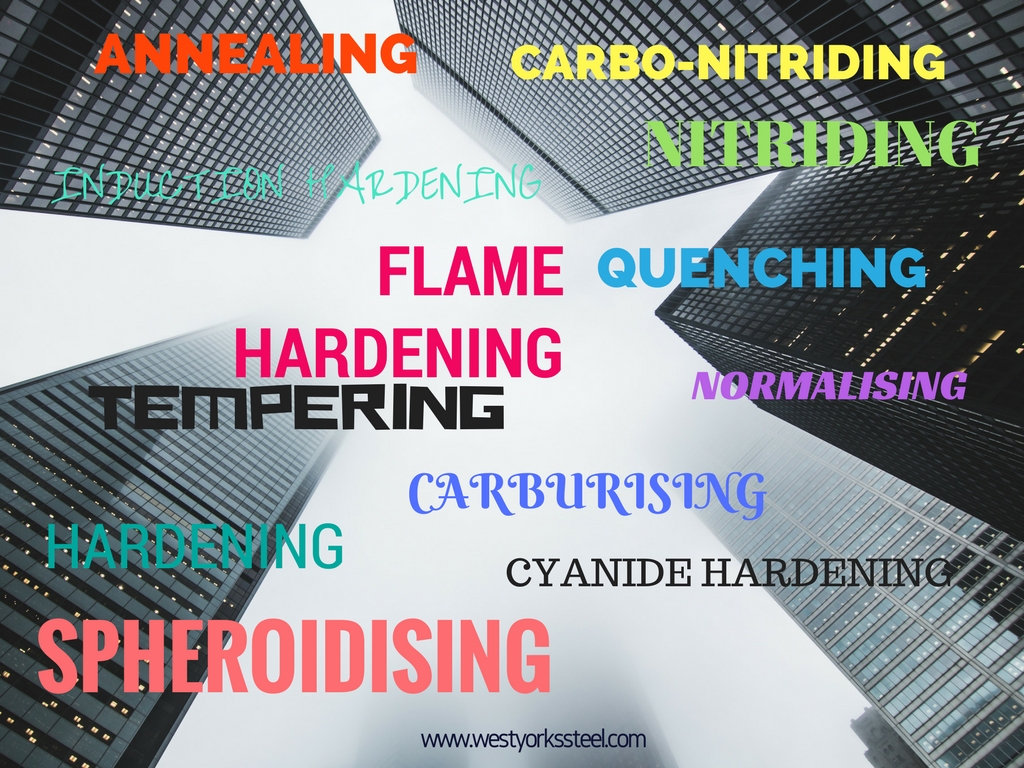
Flame hardening is also used as a means of surface hardening, but uses flames before jet-washing to quench. It’s mainly used for large items that struggle to fit in furnaces. Cyanide hardening is a way of surface hardening a steel with carbon and nitrogen, which is introduced in a bath of sodium cyanide. It works as a thin layer to create very high hardness. Carbo-nitriding is case hardening using heat, but by heating the material in a carbon and nitrogen rich environment, which diffuses the two elements throughout the surface of the steel. Nitriding works in the same way, but exclusively nitrogen instead of carbon and nitrogen. Unsurprisingly, the opposite process of allowing carbon to place itself throughout the surface is called carburising.
Once the hardening process is complete, the product needs to be tempered. Tempering heats and holds at a desired temperature and works to make the metal less brittle and bring the hardness into the correct range for the steels’ need. This is a similar process to normalising which also tries to relieve internal stresses by heating and then allowing cooling in still air.
It’s at this point, after other processes have been completed, that quenching would occur, which works to contract any heat expansion and increase the strength and hardness. For materials that would otherwise be made more brittle by this process, tempering is key.